Smart Refinery
Technology advances of modern control systems have also allowed new innovations to improve refinery reliability through advanced diagnostics. Risks are mitigated because of experience, tools and standard procedures. Specialized companies have completed thousands of migrations from a number of systems, making “risk-free migration” a reality.
Benefits of smart control systems and instrumentation are achieved during the project with commissioning, calibration and startup completed more quickly, more accurately and more efficiently. The same smart instruments continue to capture value by monitoring their own status, which allows immediate alert of abnormal asset health and the ability to predict required maintenance. Using these smart digital technologies has led to fundamental differences in the way refineries are designed, commissioned, operated and maintained.
What are the enabling technologies that permit refineries to move from reacting to predicting?
The ability to move from a reactive to a predictive reliability approach is a major component of smart refinery technology. Predictive diagnostics enable early identification of equipment problems and create “self-aware” assets and smart field devices. With today’s technologies, the cost of adding these smart devices and sensors to monitor important plant assets has decreased dramatically.
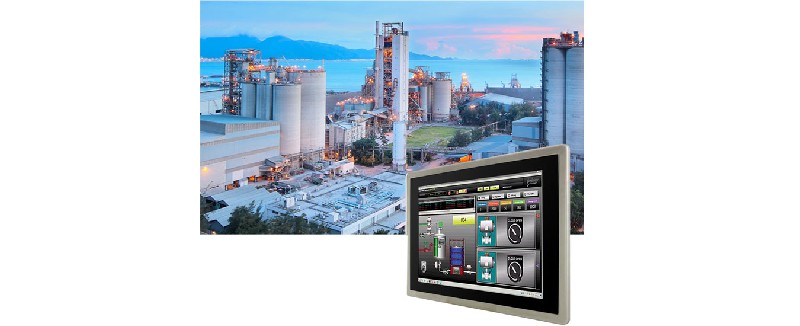
-
Smart devices analyze data in real time to provide
diagnostic information and integrate it into maintenance
procedures, providing an opportunity to act on the
information before a failure or safety incident occurs.
The reliability and safety of the entire smart refinery is
improved by preventing unplanned shutdowns.
Now a days, automation control and infrastructure protection are critical areas of any
plant operation. New control systems sometimes integrated with Safety systems, creates a unified platform that offers a single operating view of safety and automation systems in plant operations while maintaining the required separation and redundancy.
The automation solution increases process availability, production and profitability of the plant, while ensuring safety and security of personnel, equipment and the plant environment.
These projects usually have some separated parts each one has its own operation philosophy but whole the plant should be managed globally to maintain predefined function and produce the materials which the plant designed for.
For managing continues operation of Oil/Gas these fields and making stable plant, a distributed control system, as ESD system and maybe asset management systems installed to monitor and control the plant.
A Smart Refinery Control System components
There is so many different systems and methods to control a big process especially in Oil and Gas field like petrochemical or refinery plant.
• DCS System for managing normal operation of process. Monitoring and control of the system manually or automatically to have available process flow is the main role of this system.
• ESD system which responsible for managing system in emergency states to force the system to a safe status.
• PLC Systems usually used to control small packages installed for different units and then integrated in DCS system for totally management system.
•Control network which connects all distributed control systems together. Through this network all control messages will be transported with highest reliability:
• Local area network to connects different sub-systems in different
LERs
(Local Equipment Room) to Main Control Building (MCB)
• I/O Bus networks that connects control system elements to plant instruments and also system packages. These network can help us for high performance, low cost and high reliable instrument networks
• Asset Management System to manage field instruments remotely like change parameter setting, maintenance programs and so on
• Analytical software to Analyze system status, predict the future to make the best decision